5月31日,首批量产深蓝S7陆续从南京智慧工厂生产线上驶下,并同步开启了大规模的发运。从开启预售到下线发运,深蓝汽车仅用时11天就提交了一份高质量答卷,让所有人对新车背后的品牌智造硬实力有了进一步的了解。
在当下技术大变革浪潮中,智能制造、智慧工厂、工业互联网、5G、人工智能、数字化等诸多新兴技术在汽车工业的发展过程中都得到了广泛应用。作为深蓝S7的诞生地,南京智慧工厂这一行业顶尖新能源智造基地正是产业制造转型升级的代表,其不仅将深蓝品质拉向新高度,更为推动中国“智造”品质进阶贡献了强大力量。
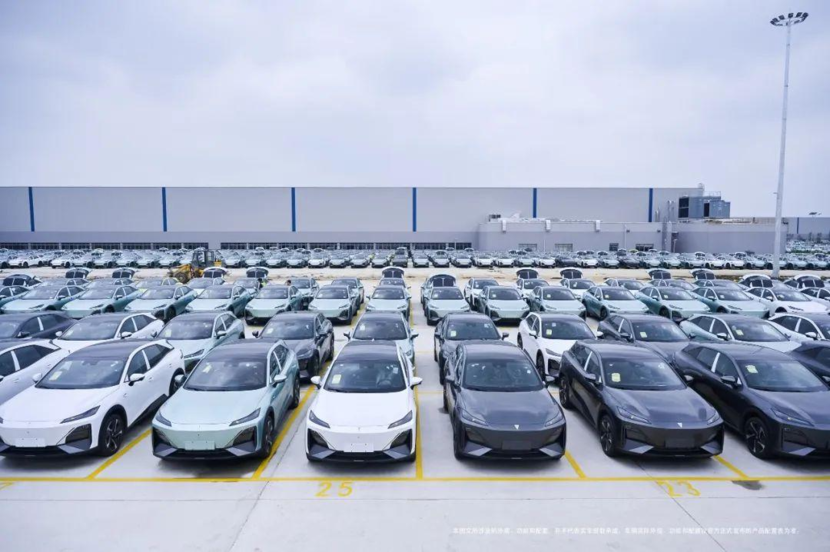
为确保极致的产品品质和高效的生产效率,南京智慧工厂在冲压、焊接、涂装、总装等每一道工序上追求精益求精,创新采用了大量自动化、智能化生产工艺,堪称全新新能源智能个性化定制示范工厂。高度自动化的智造工艺,树立行业典范
近些年,国内车企几乎都在提高生产车间的自动化程度。在这方面,南京智慧工厂为行业树立了新典范。
汽车生产车间的自动化流程主要有冲压、焊接、涂装、总装几个方面,其中冲压是对零部件的打磨,行业要求零件的误差在 ± 1mm 以内。
借助智慧工厂的大数据实时分析,深蓝汽车不但把误差要求降低到 ± 0.5mm,还实现了 98% 的平均精度,造型设计还原度提高到了 95%,而行业平均水平大约为 90%。超高的精度和严苛的要求,让深蓝汽车的还原度超过行业标准,说明深蓝自动化不但程度高,技术实力也足够强。
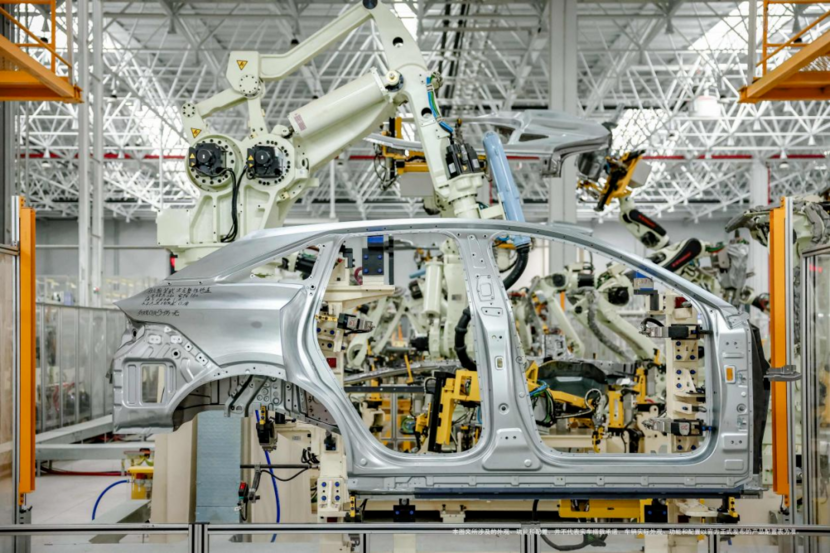
此外,冲压车间的自动装箱系统相比人工装箱管理更方便、安全更可靠、生产效率也更高。该系统主要由机器人、2D/3D视觉、皮带线、端拾器更换、盛具托盘、视频监控、AGV自动运送等系统组成,可完全实现从压机下料到进入库房的无人化生产。而且这是行业内的首次应用。
焊接方面,深蓝汽车南京智慧工厂实现了 98% 的自动化率,而行业平均水平仅为 80%~90%。在焊装车间,深蓝用 215 台机器人,2条无人生产线,覆盖了上百个工位。同时,行业首发的焊点在线检测技术,可对上千个焊点自动检测,尤其是在关重车体件表面焊点检测率达到100%,可有效规避缺焊漏焊错位扭曲飞溅等问题,保障出车质量。涂装方面,深蓝汽车南京智慧工厂自动化率为 70%,也高于行业 60% 的平均水平。
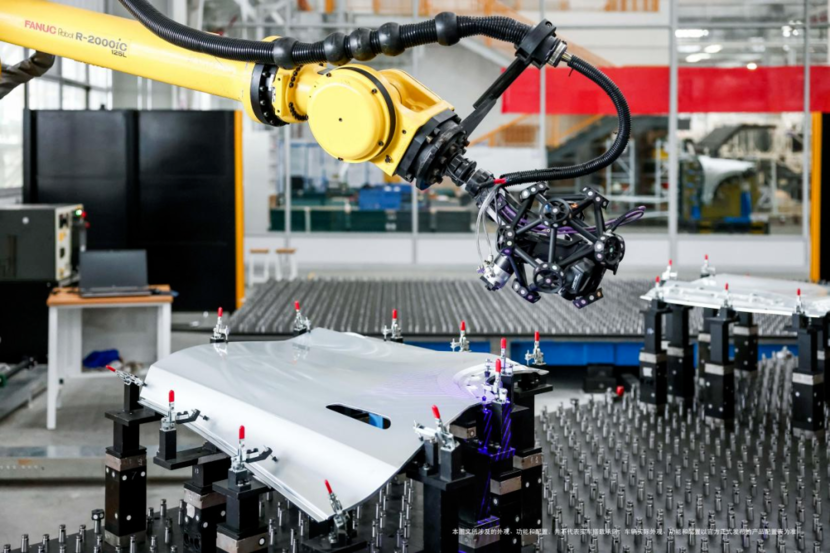
总装即汽车最后的零部件组装,深蓝汽车通过三重防错工艺(可视化、EP、精准防错)实现了大批量定制装配情况下,质量零误差。深蓝 S7 的底盘合装、轮胎装配、玻璃装备等,均实现了自动化。值得一提的是,总装车间还首次引入智慧物流系统实现来料自动拆托、存储、配送上线,自动化率高达62%,领先行业,让物流区域也变成“无人区”。
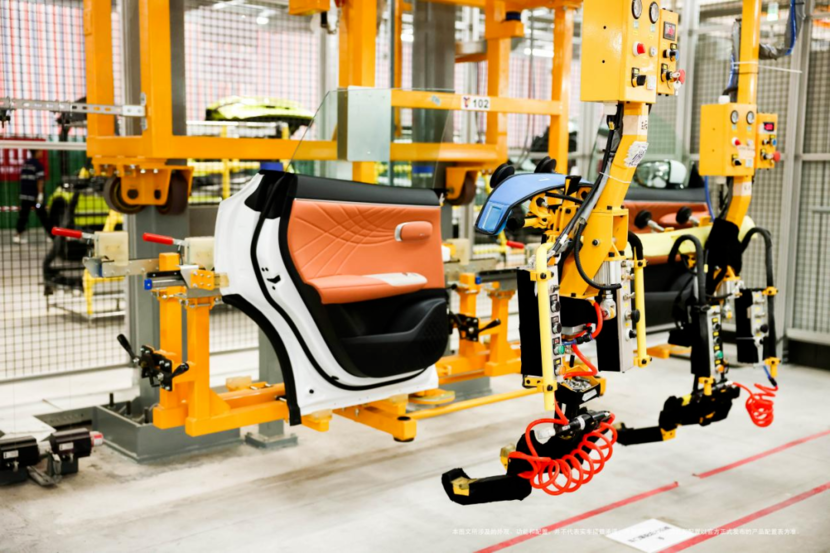
严控高品质、保证高效率,深蓝加速实现高质量发展
在融合传统汽车制造业与智能制造优势的同时,南京智慧工厂实现了“无死角”的产品质量把控,打造了能够满足极致严苛标准的质管体系,为高品质产品开发持续保驾护航。从零部件原材料到整车交付,过程中共设置11道质量墙,层层围堵,确保每一台车都是高品质交付。
四大车间环环相扣,严把质量关的同时,深蓝汽车真正做到了高标准、高效率生产,为后续交付提供了保障。通过深度应用智能制造技术,贯通5G网络与物联网平台,制造顺序化率达90%以上。另外,工厂也构建个性化定制模式下的业务及数据架构,贯通个性化选车、智能排产、协同制造、精准交付等环节,OTD交期承诺仅16天。
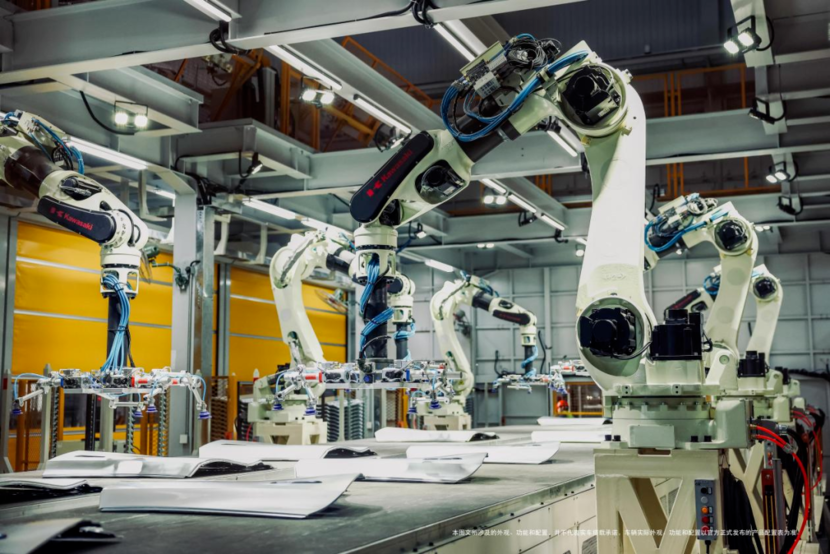
写在最后
毫无疑问,智慧高效的顶级智造基地为深蓝品质保驾护航,让业界对深蓝S7以及深蓝品牌充满了信心。相信随着南京智慧工厂正式走向台前,深蓝汽车将迎来新起点,品牌在新能源汽车领域的布局也将加速迈向高质量发展新时代。
网友评论